Pultrusion is an automated process. It allows the continuous production of profiles manufactured with high performance composite materials.
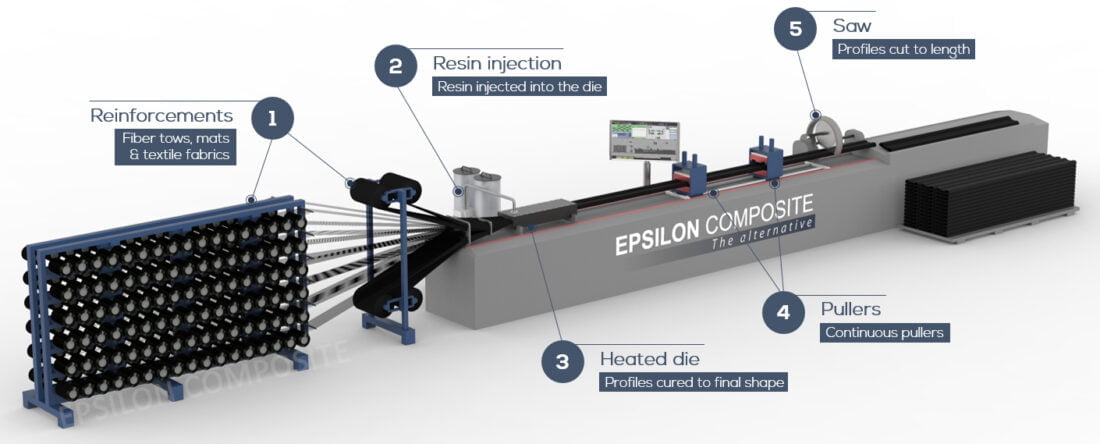
Carbon fiber pultrusion is at the core of Epsilon’s Composite business in its factory in Gaillan Médoc (France) . Since 1987, the compagny is the number one worldleader in carbon fiber pultrusion.
“Pultrusion” stems from the contraction of “Pull” and “Extrusion”. Extrusion is a continuous manufacturing process during which matter (plastic or metal) is pushed through a die of a given shape. With pultrusion, matter is simply pulled through a heated die where resin is polymerized (instead of being pushed) giving the profiles their shape and final properties. At the end of the production line, the pultruded profiles are automatically cut at the desired length.
Thanks to pultrusion we can efficiently and industrially manufacture high performance composite parts with optimal quality :
- A very high fiber rate (60 to 75 % in volume, versus 50 to 55 % for most other composite manufacturing processes),
- A low permeability level (<2% in volume),
- An optimal fiber alignment according to the desired angles (from 0° to 90°),
- An excellent surface appearance which does not require machining or finishing (“net shape”),
- Excellent reproductibility from one production to another.
Thanks to 24/7 production, this manufacturing process guarantees high yields.
We use spools (carbon, glass, aramid or natural materials) and resin components (base, hardener, accelerator and additives) as raw materials. This insures flexibility and optimized production costs compared to the use of textile fabrics or prepregs.
Want to know more about the process ? Watch our video about pultrusion.
Thermosets and thermoplastics
According to our experience, thermosetting resins (from the epoxide family) are usually the best compromise for performance, durability and costs in pultrusion. However, it’s also possible to manufacture thermoplastic composite materials in pultrusion. For example, to benefit from better recycling properties or other specific properties (impact or fire resistance, weldability…). From the early 90’s, Epsilon Composite developed thermoplastic pultrusion for the aerospace sector. The compagny continues to innovate and incorporate the latest industry advancements in order to provide its clients with the most suitable materials.
Pultrusion line variants
Pultrusion has different variants such as “Pullwinding”. Pullwinding makes it possible to manufacture composite tubes with personalized fiber laying angles. Moreover, it is also possible, through this process, to produce kilometer long products in the form of spools. Thus, allowing the simultaneous production of 8 profiles per production lign.
