International Day of Human Space Flight
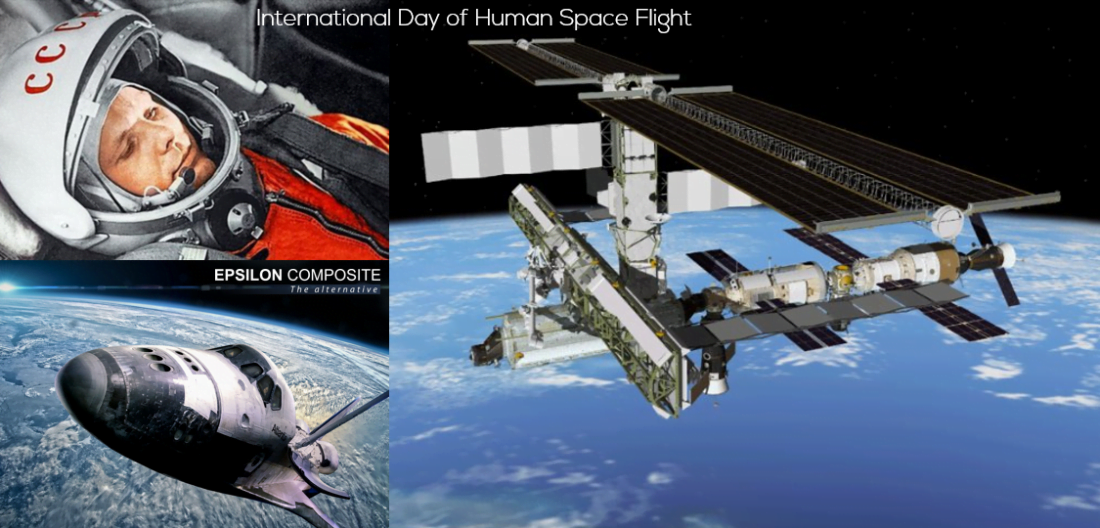
On April 12 1961, Soviet cosmonaut Yuri Gagarin became the first Human in space when he orbited the Earth in a Vostok spacecraft. NASA’s cosmonaut Alan Shepard Jr replicated his feat about a month later, when he was launched aboard Mercury-Redstone 3.
60 years later, more than 600 people have now been to space, and the pace is accelerating as technology and innovation greatly facilitated space missions
Composite materials played a key role in the success of space operations, as composites can be found on human spaceflight vehicles, satellites and payloads, as well as on the launch vehicles that are used to get them to space.
Composites greatly contributed to make space crafts lighter and more efficient, which allowed to increase their payload and reduce the amount of fuel required to propel them on orbit.
They also made space crafts more reliable, thanks to their outstanding thermal stability. Composite applications in this field include filament wound rocket motors and pressure vessels for fuel and gas storage, optical benches, RF and solar arrays support structures, and of course composite struts and booms, products for which Epsilon Composite has developed an expertise for more than 20 years.
In terms of materials, high strength or high modulus carbon fibers and epoxy resins are extensively used for their stiffness, lightness and dimensional stability. Low moisture absorption resins such as cyanate ester are also widely used.
On the other hand carbon-carbon, carbon-ceramic or carbon-phenolic composites are generally used for high temperature components in rocket nozzles, reentry heat shields, Thermal Protection System supports. Ablative composites can be used as an endothermic sacrifical layer, as they absorb heat by changing state (actually, the Apollo capsule heat shield was probably the first significant use of composite materials in space).
While costs and production capacity were not a major concern for the space industry historically, this has drastically changed in the recent years, and more and more players are turning their head towards the benefits of Pultrusion for their space programs… That’s because Pultrusion is an automated out of autoclave manufacturing process, which allows to produce kilometers of high performance composite profiles in a cost effective way. Those profiles can then be machined and assembled into finished parts and structures.