Our carbon fiber technical rollers help increase machine productivity and production quality, thanks to their ultra-light yet rigid design. Every year, Epsilon Composite manufactures over 30,000 carbon fiber technical rollers for its customers worldwide, with a comprehensive range covering a wide variety of applications.
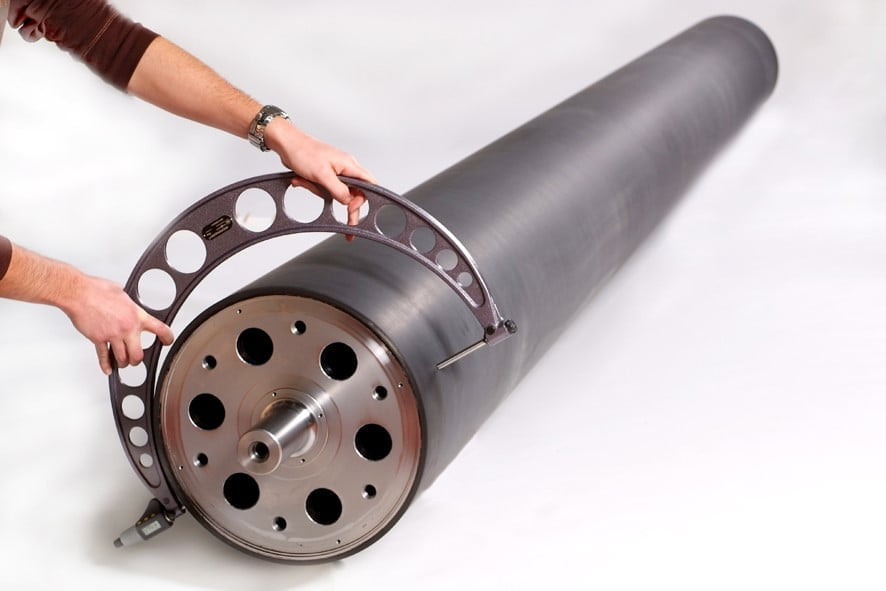
Epsilon Composite offers a complete range of standard and custom carbon fiber rollers for a wide range of applications:
- Carbon rollers for printing: rollers for offset, digital, gravure or flexographic printing (carrier shafts, pneumatic and hydraulic bridge adapters, anilox and doctor blade chambers).
- Carbon rollers for technical films: guide rollers, contact and tension rollers, detour rollers, drive rollers, lamination rollers, coating rollers, brush support rollers and specific rollers for manufacturing, cutting, coating and converting technical films…
- Carbon rollers for nonwovens: carding rollers, crosslapper rollers, needling rollers…
- Carbon fiber rollers for the electronics industry: conveyor and guide rollers for the manufacture of printed circuit boards (PCBs), flat screens (LCD, plasma, etc.), etc.
Our carbon fiber rollers are manufactured using 2 patented processes:
- Pullwinding (a variant of pultrusion), which optimizes the manufacture of carbon tubes with optimal mechanical properties, thanks to customized fiber orientation.
- K1, which combines the advantages of pultrusion and filament winding, generally for producing large-diameter tubes in small to medium-sized series.

Technical composite rollers: a superior alternative to traditional solutions
Lighter and stiffer than traditional metal solutions, our rollers will allow better productivity of your machines: they will be able to operate at higher speed and/or be wider. Thanks to a stiffness up to 2 times higher than steel, carbon rollers can run at high speed without risk of vibration and with less deformation, thus maintaining an optimal production quality.
Our rollers undergo a precision grinding and are dynamically balanced in 3 planes to optimize their precision and performance.
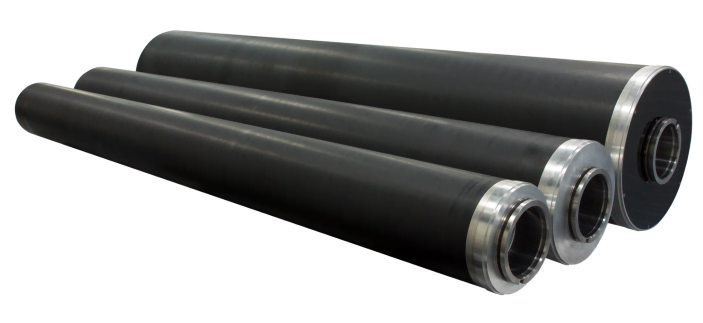
Key features of our technical composite rollers:
Diameter | Up to Ø700 |
Length | Up to 12m |
Stiffness | Up to 400 GPa |
Surge | TRI (Total Indicator Run-out) up to 5 µm / 5 m |
Fittings | Metallic, plastic, composite |
Machining of rollers | Roughness: option to choose the surface finish |
Cylindrical, concave, convex machining, etc. | |
Single, double grooves, etc. | |
Surface coating | Raw from pultrusion |
Elastomer: PU, EPDM, NBR, etc. | |
Specific composite coating: surface veil, fiberglass, gelcoat, etc. | |
Metallic: chromium, tungsten carbide, etc. | |
Operating temperature: | Up to 80°C standard and higher than that on request |
Conductivity | Insulating, antistatic or conductive surface in accordance with ATEX 95 |
Chemical resistance | On request: option to offer rollers capable of operating in various environments (basic, acidic, etc.) |
