Composite struts (or “rods”) are a durable and lightweight solution to transfer forces or movements within a structure: civil engineering structures, giant telescopes, machines, aircraft, etc.

Different uses for struts
Whether in aeronautics, civil engineering, robotics, defence or industry in general, carbon struts are a key component, as they perform two essential functions: structural reinforcement and motion transmission.
These critical components are often subject to stringent specifications: stiffness, resistance to very high loads, impact resistance, weight optimization, dimensional stability at any temperature, resistance to environmental aggression (corrosion, UV, kerosene, etc.)
In robotics, the carbon struts are used to transmit extremely fast movements (several cycles per second) and therefore undergo accelerations up to 8G, while maintaining an accuracy lower than a millimetre for the effector.
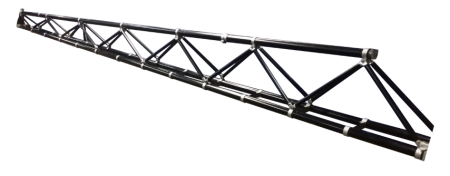
For each application, there is a strut solution
In order to meet these very diverse markets and high requirements, Epsilon Composite has developed a whole range of solutions:
- Hybrid struts, composed of a carbon tube obtained by pultrusion; metal end-fittings applied by bonding or mechanical anchoring. Bonding is the most common solution because it offers the best reactivity and costs on small and medium series. The anchoring of the tip by overmoulding a thermoplastic composite is a solution patented by Epsilon Composite to avoid bonding. This is particularly useful for large series and for critical applications where it is best to avoid special processes (such as bonding).
- 100% composite struts: full composite struts obtained by assembling several pultruded profiles, or by overmoulding a thermoplastic composite end cap. These solutions limit the weight and eliminate corrosion problems.
In addition to fixed length struts, Epsilon Composite also offers adjustable composite tie rods, on which threaded rod ends allow the length of the rod to be adjusted in order to compensate gaps in a structure or adapt to installation constraints. These solutions are particularly used in the aeronautics, space and automotive sectors.
Our teams of experts will guide you towards the most appropriate solution for your needs.
Case Study
Reconstruction of the roof of a historic structure, the Clos des Cordeliers