Epsilon Aerospace has developed and qualified a wide range of rods, profiles and sub-assemblies for aeronautical and space applications.

Founded by two materials engineers from the French aerospace industry, Epsilon Composite has been a supplier to the aerospace industry since its inception, initially mostly for structural applications for military aircraft (aircraft and helicopters) and satellites.
In 2009, Epsilon Composite launched a structured Research & Development approach to meet Airbus’ needs (and in particular those of the A350 XWB).
It required the development of materials and processes that meet aeronautical requirements, including:
- Fire resistance
- Impact resistance
- Detectability of impacts
- Chemical resistance
- Protection against galvanic corrosion
- Full traceability
- Geometric repeatability
- Non-destructive testing
- Mastery of special processes (NADCAP, etc.)
After several years of effort by our teams and massive investments, Epsilon Aerospace can claim a number of major successes on ambitious developments—while also ensuring deadlines were met and the customer’s budget adhered to—which have led Epsilon Composite to become a tier 1 supplier of Airbus.
EPSILON AEROSPACE COMPOSITE STRUTS
- Adjustable rods (tie rods, flight control rods, etc.)
- Monolithic full carbon struts (center wing box, floor beam struts, etc.)
- Hybrid struts with carbon tube and bonded metallic end-fittings (floor support, engine mounts etc.)
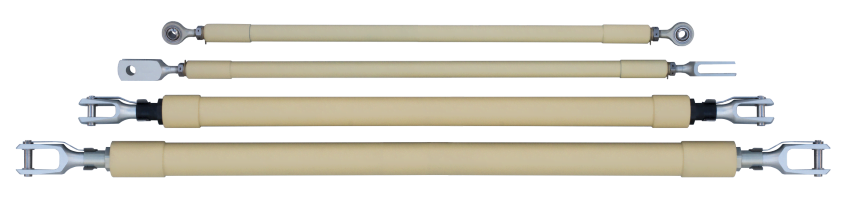
PROFILES AND SUB-ASSEMBLIES
Thanks to the mastery of an industrial continuous manufacturing process, out of autoclave and using only raw materials, Epsilon Composite is able to meet the requirements of aircraft manufacturers and equipment manufacturers in an extremely competitive manner, to supply primary or secondary structural parts as well as interior cabin parts.
The parts and sub-assemblies produced by our teams can therefore advantageously replace metallic solutions (aluminum, stainless steel or titanium) as well as traditional composite solutions (pre-pregs, filament winding, etc.).

OUR SOLUTIONS
- Weight savings through the replacement of metallic parts at competitive prices.
- Cost reduction compared to traditional composite processes.
- Complies with FAR25 fire resistance standards (“FST”)
- Integrated protection against galvanic corrosion.
- High temperature resistance (up to 230°C).
- Excellent resistance to ageing in wet environments
- Impact resistance and damage tolerance
- Design of complex solutions & composite engineering (“Design & Build”)
- Management of complete qualification tests,
- 5-axis machining on large parts
- Assembly & installation
- Structural bonding
- Overmoulding of thermoplastic composites
- Rapid prototyping workshop.